Lighting the way towards smarter production
By harnessing the power of 4IR, three Aramco facilities granted ‘Global Lighthouse’ status show how smarter, safer, and more-efficient energy production can be possible.
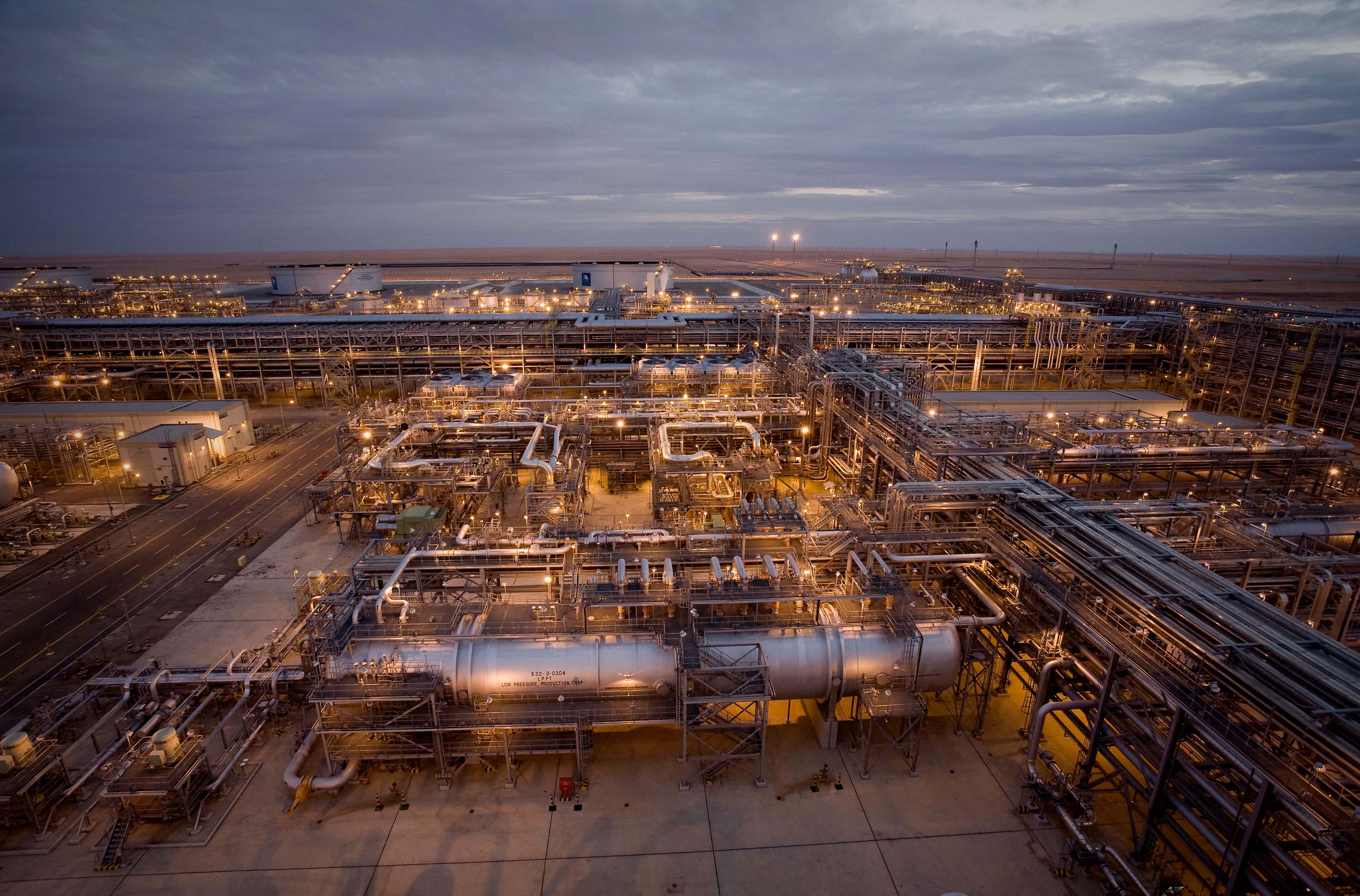
- Fourth Industrial Revolution technology (4IR) offers improvements in operational and business performance, across almost every aspect and type of industry
- Our 'Uthmaniyah, Khurais and Abqaiq facilities integrated digitalization into their operations to make them safer and more efficient through data-led decision making and smart, integrated technologies
- These sites are part of a select group of world-leading production facilities granted ‘Global Lighthouse’ network status by the World Economic Forum for their pioneering use of 4IR
Fourth Industrial Revolution (4IR) technology offers dramatic enhancements to operational and business performance at a pace never before seen, in almost every aspect of industry. Its transformative power comes from connecting real world machines, vehicles, and physical products to digital systems like artificial intelligence (AI), data analytics, and the Internet of Things (IoT).
That means factories can automatically adjust production to meet demand, as well as predict faults, and initiate preemptive repairs. It allows for robots or computers to take on repetitive, time-consuming and hazardous tasks, potentially freeing-up time for employees to undertake other useful tasks.
A community of 4IR pioneers
Globally, businesses involved in manufacturing and processing still lag behind those in other sectors in their adoption of 4IR. More than 70% of companies are still at the pilot stage of digital transformation, according to research carried out in 2020 by the World Economic Forum (WEF) and McKinsey.
To close this gap, and accelerate a more comprehensive adoption of advanced technologies in production processes, the WEF has set up the Global Lighthouse Network (GLN). The GLN showcases companies that are pioneering the use of 4IR to transform factories, value chains, and business models.
Three of Aramco's facilities have been made a part of the GLN for their initiatives in integrating 4IR technology.
Abqaiq Plants — The third Aramco facility to be awarded Global Lighthouse status.
Technology leaders working together
Through the GLN, the WEF aims to demonstrate the potential of 4IR technology by highlighting facilities that have successfully implemented it.
Being accepted into the network is a rigorous process. Each application is assessed by a committee of industry experts, who then visit the leading candidates, in-person or virtually, to inspect their implementation of 4IR technologies. This committee possesses first-hand knowledge of the world’s leading 4IR facilities and considers the complete production and value chain. It assesses not only the technological innovation of the prospective network member, but also whether it is prioritizing both planet and people in scaling its business.
Once admitted, facilities become part of a community, connecting and communicating to share best practice. Members collaborate on new projects and develop insights, learning together and incubating new partnerships.
This is important for Aramco as we continually strive to leverage partnerships to drive innovation and meet the world’s growing energy needs more efficiently. Attempting to balance energy production and increased sustainability demands more efficient oil and gas processing and production. That is where pioneering technologies offer a way forward.
The world's first Global Lighthouse oil & gas facililty
In 2019, our 'Uthmaniyah Gas Plant (UGP), one of the world’s largest gas processing plants, was the first Aramco facility to be granted Global Lighthouse status. It is also the first oil and gas facility in the world to be included.
A key reason for this was the gas plant’s application of 4IR technologies to transform the workplace experience for employees. UGP made use of wearable technology to boost production and transform safety.
'Uthmaniyah Gas Plant — The first Aramco facility to be recognized by the World Economic Forum.
A sensor worn on a smart watch, or an identity badge worn by a worker on-site, can track valuable information. Tracking the wearer’s vital signs, for example, can warn them if they are at risk of heat exhaustion.
Similarly, a gas leak, though rare, can be very dangerous to workers in confined spaces. Hazardous gases can be both invisible and scentless, but a wearable sensor can detect other properties and sound an alert telling the workers to get to safety.
UGP also uses drones to make facility inspections faster and safer. Using a drone to inspect the top of a tower means a staff member does not have the safety risk of working at height, and it saves the site the cost and time involved in constructing scaffolding. Instead, an individual can remain on the ground and remotely pilot a drone up to the inspection point, where cameras can check that all is well.
The world's largest intelligent oil field
The second of our facilities accepted into the Network was Khurais, the world’s largest intelligent oil field, in 2020. Khurais opened in 2009 and has turned to 4IR technologies to help manage its sheer scale: over 500 oil wells. Tens of thousands of sensors have been installed across Khurais to collect data on every aspect of production and power consumption.
All this data feeds into a ‘digital twin’ of Khurais. This is a real-time virtual model of the facility that monitors performance, and predicts and diagnoses any problems within the end-to-end operations.
A digital twin gives engineers the ability to test planned or proposed adjustments to plant operations in a virtual environment and deploy the most effective ones. This can be done without any disruption to the activities of the real plant.
The technology has helped us to increase production at Khurais, while simultaneously reducing power consumption by 18%, reducing our maintenance costs by 30%, and cutting inspection times by around 40%.
Khurais oil field — The world’s largest intelligent oil field.
A digitized, 70-year-old facility
Abqaiq Plants is our largest oil processing facility and one of the largest crude stabilization plants in the world, providing 5% of global oil supplies. It is also our oldest, at over 70 years old. By utilizing cutting-edge technologies, we transformed its manufacturing processes, making them more digitalized. The consequent boost in its performance and efficiency, resulted in it becoming our third facility to be awarded Lighthouse recognition in 2021.
An old facility does bring challenges, however. The buildings were not constructed with Wi-Fi in mind, for example, but data transfer is vital for smarter production. That has meant spending time putting new infrastructure into the facility — from wires to new walls — to enable fast and reliable connectivity.
Abqaiq Plants is Aramco’s largest oil processing plant
Abqaiq Plants is in close proximity to the Ghawar Intelligence Center, which acts as a 4IR information hub across several fields. It provides support and benchmarking tools to Abqaiq Plants, Khurais, and other facilities, so they can compare their 4IR processes. The Center also develops its own applications, including predictive analytics tools based on IoT data.
Impressive impact with AI
Abqaiq Plants has been able to increase power generation from the oil it produces, simply through employing AI algorithms that analyze the oil stabilization process, and then make adjustments in order to optimize performance and improve product consistency.
Similarly, sensors and AI have been used to predict when assets might fail and to schedule maintenance or replacement. The result has been a drop in unplanned maintenance of 20% and the significant reduction of production delays due to equipment failure.
Furthermore, the technology has helped us reduce gas flaring, the process of releasing and burning off excess natural gas, that is sometimes necessary as a safety measure, but which we work to constantly reduce because it releases methane and carbon dioxide.
AI helped us improve processes at Abqaiq Plants
An exciting future for industry
We aim to become among the world’s leading digitalized energy companies by adopting 4IR technologies to transform our operations. The presence of three of our facilities in the Global Lighthouse Network demonstrates how seriously we take that goal.
The innovations of 4IR technology are unfolding with unprecedented speed and will forever change the way we work.
The potential for these technologies to make industry more efficient, more productive, and more sustainable is exciting. The coming years will see the pace of change increase further, promising innovations that we are only just beginning to imagine, with our three Global Lighthouse facilities lighting the way.
More from Elements
The material in this article is intended to be for general informational purposes only, and readers should not place undue reliance on the statements or opinions therein. Any information provided speaks only as of the date this content was published and Saudi Aramco undertakes no obligation to correct, update, or revise any statements or opinions made in or implied by this article.