Big data, big insights
How new technological applications are lowering energy intensity and cutting emissions at Aramco.
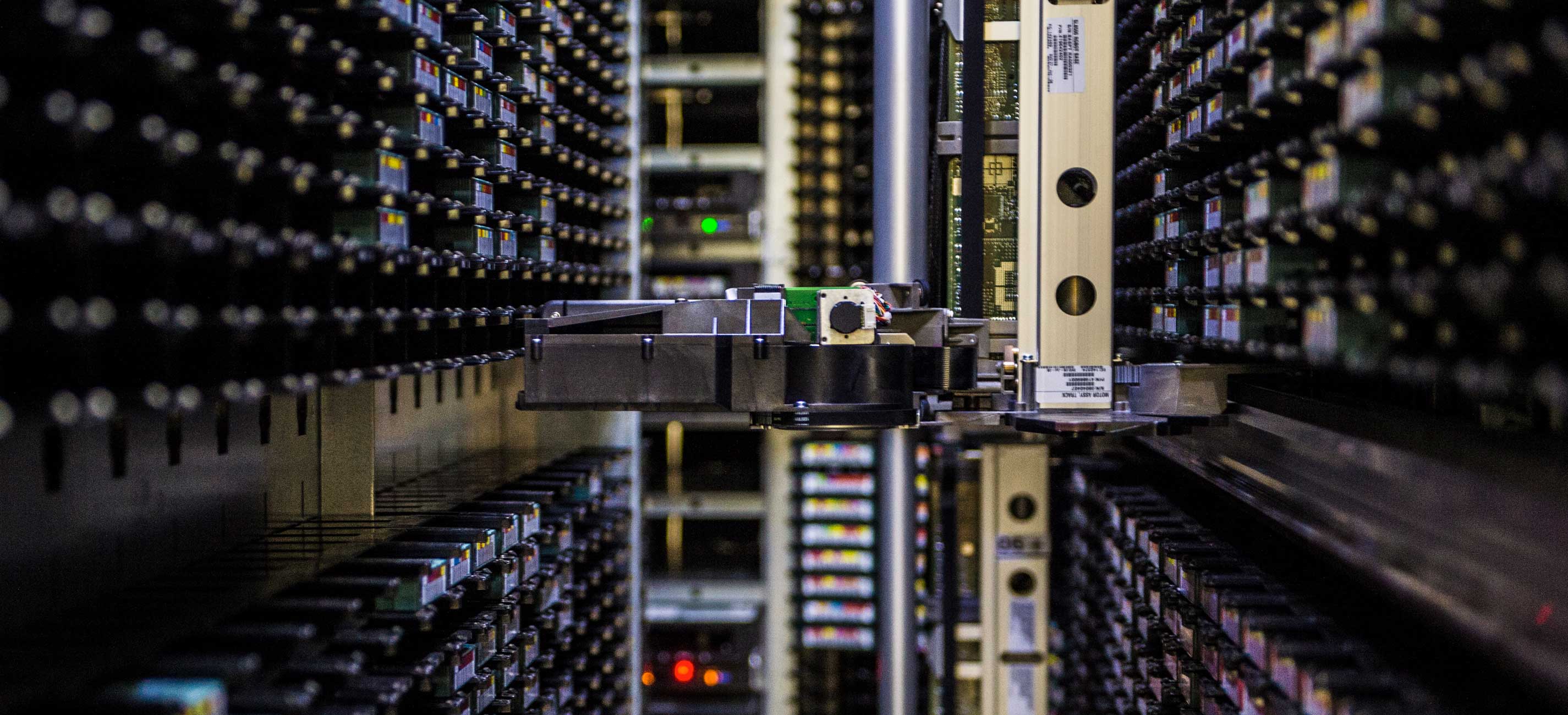
- Big data leverages the power of modern computing to drive greater efficiency
- The approach is successfully optimizing oilfield operations and maintenance
- Through data-driven predictions, Aramco is reducing energy use and minimizing flaring
The capture and analysis of large volumes of data, otherwise known as “big data,” has produced sweeping solutions to complex problems. This technology helps us to mine colossal amounts of information to identify patterns — and then predict what will happen next.
Big data can forecast the weather, prevent cybercrime, and develop new medicines. And, alongside other machine learning and artificial intelligence (AI), it’s revolutionizing how many sectors operate.
This includes oil and gas, where big data presents huge opportunities. Already, it’s amplifying efficiency and production, reducing emissions, and enhancing operations at every level. And similar techniques can unlock breakthroughs along the entire energy-production chain.
Here’s how.
Where drones prowl, walls animate, and every barrel is tracked
Teams of data scientists design and implement complex analytics at Aramco’s 4IR Center (4IRC) in Dhahran. This advanced research and operations hub brings together a suite of digital technologies under one roof.
The facility spans 2,500 square meters of office space. Upon entering, visitors are greeted by a “V-receptionist,” a hyper-realistic hologram that explains the safety protocol. Further into the facility, the surroundings come alive — as the 279 square meters of video walls display animated feeds. At its heart, the AI Hub, encircled by a concave display screen, crunches algorithmic formulae at superhuman speed.
Every day, the 4IRC receives more than 5 billion data points, generated from Aramco’s operations across the Kingdom, as well as access to millions of engineering drawings, and inspection and maintenance data. Combining this operational big data with the available computing power, state-of-the-art AI and machine learning tools, the Center is able to translate the data into actionable insights, which help predict and improve asset performance, safety, and reliability.
Powered by data, Aramco robots take to the air, land, and sea, detecting methane levels, tracking inventory, and inspecting underwater assets.
The Company’s robots — such as SWIM-R (Shallow Water Inspection and Monitoring Robot), an aquatically adept mechanical arm developed in-house — work alongside other cutting-edge robotic technologies, which the Company has adopted. Powered by data, these machines take to the air, the land and the sea, detecting methane levels, tracking inventory, minimizing confined spaces entry, and inspecting underwater assets.
Ahmad Al-Othman, division head of Advanced Process Solutions, which manages the 4IRC, says; "The Center, powered by our young and talented people, plays a major role as the corporate digital think tank — exploring and discovering new opportunities, innovative ways of using 4IR technologies, and solutions to drive excellence and create value for the Company.
“The Center, powered by our young and talented people, plays a major role as the corporate digital think tank — exploring and discovering new opportunities, innovative ways of using 4IR technologies, and solutions to drive excellence and create value for the Company.”
Ahmad Al-Othman, division head of Advanced Process Solutions
An extensive network in a challenging environment
Aramco’s energy infrastructure is among the most extensive in the world. It also operates in some of the hottest temperatures on the globe.
Both these facts present major challenges for any analytics system, as the scale of data capture involved is huge. High summer temperatures can make the fluids in pipelines and plants more volatile — and therefore more challenging to monitor and control.
Aramco’s energy infrastructure operates in some of the hottest temperatures on the globe – a challenge that Aramco overcomes through the use of advanced analytics.
In addition, such systems do not come “off the shelf.” Rather, they must be tailored carefully to the specific context and assets involved.
“In the past, data collection and analysis were done by experts monitoring the facilities manually. The data for each plant was then analyzed on site, limiting our ability to enhance performance,” says Alaa Alahmed, who focuses on managing energy use at midstream facilities. “But establishing big data systems was only made possible by working closely with experienced engineers on the ground, as they were already familiar with their respective plants and operating conditions.”
To introduce the big data systems, the first step was to digitize and capture vast amounts of information amounting to approximately three million data points per day across the facilities.
According to Alaa, to introduce the big data systems, the first step was to digitize and capture vast amounts of information amounting to approximately three million data points per day across the facilities. All of this information was then processed — and is now monitored.
Ahmad Almulhim, who leads the 4IRC team managing this big data project, believes the new system’s greatest strength is its real-time operation.
“Now, if indicators stray outside predefined targets, facilities are automatically notified — immediately. This enables rapid remedial action to maintain optimum performance,” he says.
His team has developed algorithms to manage energy consumption and set targets based on historical data for energy intensity, flare emissions, and crude quality at all of the 30-plus sites and more than 50 facilities involved.
How data predicts the future
Big data unlocks enormous benefits. A plant that is outperforming others, for example, can be easily spotted, and their improved operational practices applied across the board.
Flaring, the release and combustion of hydrocarbon gases due to the buildup of pressure in the pipeline and processing facilities, is also being tackled by big data, as this technology allows the engineer in charge to visualize the entire system at once. This vantage point makes it easy to quickly identify the source of flaring — and then generate potential solutions.
So far, the use of big data has led to a reduction in flare emissions of 50% since 2010; flaring intensity remains at less than 1% of Aramco’s gas production.
And big data can even look into the future.
Yousef Aloufi, who focuses on flare minimization at Aramco, says he relies on 18,000 sources of data to monitor and forecast future flaring.
“By comparing the real-time data to models built up with big data using various techniques, including deep learning, the system can predict when a facility is going to exceed its flaring targets, and remedial action can be taken well in advance,” he says.
According to Yousef, this will also enable future operating targets to be set on the basis of careful analysis.
Aramco’s team of data scientists and subject matter experts is continually identifying ways to more effectively utilize big data. This includes the use of detailed computer simulations of each facility. These models also allow our experts to test various scenarios virtually.
Predictive maintenance, for example, spots when a component is going to fail in advance by first modelling its behaviour, and then forecasting its future performance. Now, a replacement can be installed before the component wears out. (Such predictive models — also used extensively in manufacturing industries — are often known as its Digital or Virtual Twins.)
Aramco has also automated the decision-making of its electric submersible pumps (ESPs) across its oil fields. Previously, the speed of these pumps was overseen manually — meaning an operator would visit the well site and adjust the velocity by hand. Now, at Khurais oil field, prescriptive analytics modulate this speed automatically to ensure optimal operation, which has scaled up 400+ wells at the site, reducing energy consumption by up to 20%.
To help reduce the impact of flaring, video streams of the flame are analyzed to monitor any changes in smoke emissions and flame height. The deep learning process takes thousands of images of flaring stacks and compares them to CCTV of the same flame in real time. Using what are called convolutional neural networks (CNNs), this technology can predict how much smoke will be generated. As well as minimizing flaring, this enables Aramco to move toward smokeless flames, which avoids localized pollution and further reduces any wider impact on the environment.
The tip of the iceberg
The automation of data collection and analysis — along with predictive modeling — has generated significant improvements in energy and carbon intensity, safety management, and overall cost and efficiency.
But we’re only seeing a sliver of the full potential.
Big data gathered from newly digital oil fields will provide for an entirely new kind of energy chain — one that can be efficiently managed and automated, while lining the system up to benefit from further advances as computing power keeps expanding.
It’s been said that data — a trapped resource that is valuable to extract — is the new oil. If we extend this analogy to AI, then it’s easy to see it as the electricity, the power that moves progress. Both are housed at the 4IRC, where cutting-edge technology makes new insights to optimize industry engines. Armed with this new information, the entire operation is running smarter and cleaner, every day.
Because from big data comes big insights.
More from Elements
The material in this article is intended to be for general informational purposes only, and readers should not place undue reliance on the statements or opinions therein. Any information provided speaks only as of the date this content was published and Saudi Aramco undertakes no obligation to correct, update, or revise any statements or opinions made in or implied by this article.